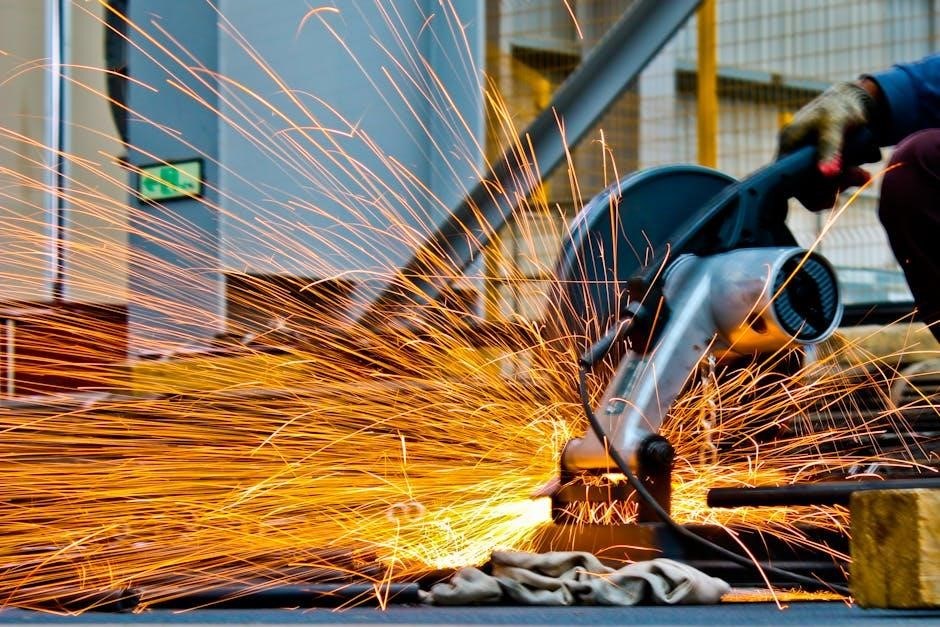
Allen-Bradley 1756-EN2T Manual: An Overview
The Allen-Bradley 1756-EN2T manual provides comprehensive instructions for installing‚ configuring‚ and operating this EtherNet/IP communication module. It serves as a vital resource for understanding the hardware and network integration aspects of the module. This manual includes key details for effective use.
Installation Instructions
The installation instructions detail the steps for physically setting up the 1756-EN2T module. This includes module placement‚ network address configuration‚ and secure connection to an EtherNet/IP network‚ ensuring proper functionality and communication within the control system environment.
Module Slot Location
Determining the correct module slot location is a crucial first step when installing the 1756-EN2T module. Proper placement within the ControlLogix chassis ensures reliable communication and avoids potential conflicts with other modules. Refer to the chassis documentation for specific slot compatibility guidelines and restrictions. Consider factors such as power requirements‚ communication bus assignments‚ and any existing module configurations. Ensure the selected slot is free and compatible with the 1756-EN2T’s communication interface. Incorrect placement can lead to system errors or failure. Always consult the ControlLogix system manual for detailed instructions and diagrams illustrating proper module placement within the chassis to guarantee optimal performance and system stability.
Network Address Configuration
Configuring the network address for the 1756-EN2T module is essential for establishing communication within the EtherNet/IP network. This involves assigning a unique IP address‚ subnet mask‚ and gateway address (if required) to the module. The IP address must be within the same subnet as other devices on the network to facilitate seamless data exchange. Use software tools like RSLinx to discover the module and access its configuration settings. Ensure the assigned IP address does not conflict with any existing devices on the network to prevent communication errors. Double-check the subnet mask to match the network configuration. A correctly configured network address ensures reliable connectivity and data transfer between the 1756-EN2T module and other devices.
Module Installation Procedure
To install the 1756-EN2T module‚ first‚ power down the ControlLogix chassis. Locate the appropriate slot for the module‚ ensuring it aligns with system design. Remove the slot filler from the chosen slot. Carefully align the module with the backplane connectors and firmly press it into the slot until it is securely seated. Verify the module is properly latched to prevent accidental dislodging. After installation‚ power up the ControlLogix chassis. Monitor the module’s status indicators for correct operation. If the module isn’t recognized‚ double-check the installation and connections. Proper installation is critical for stable and reliable communication. Refer to the 1756-EN2T manual for specific torque values and additional safety guidelines to ensure a secure and safe installation process.
EtherNet/IP Network Connection
Establishing an EtherNet/IP network connection with the 1756-EN2T module involves connecting an Ethernet cable from the module’s port to a network switch or directly to another EtherNet/IP device. Ensure the cable meets Cat5e or higher standards for optimal performance. Verify that the network switch is properly configured and supports EtherNet/IP protocol. Assign a unique IP address‚ subnet mask‚ and gateway address (if needed) to the 1756-EN2T module using configuration software like RSLinx. Test the network connection by pinging the module’s IP address from a computer on the same network. Proper network configuration ensures seamless data exchange between the 1756-EN2T module and other EtherNet/IP devices‚ facilitating reliable communication within the industrial automation system. Secure the physical connection.
USB Port Programming
The 1756-EN2T module features a USB port that facilitates direct programming and configuration. Connect a USB cable from your computer to the module’s USB port. Open RSLinx Classic software and establish a communication path to the module through the USB driver. This connection allows you to configure the module’s IP address‚ subnet mask‚ and other network settings. You can also use the USB port to update the module’s firmware. Ensure that you have the correct drivers installed on your computer for the USB connection to function properly. The USB port provides a convenient method for initial setup and troubleshooting‚ bypassing the need for a direct Ethernet connection during the programming phase. Disconnect after configuration.
Module Compatibility
The 1756-EN2T module offers compatibility with various ControlLogix controllers and other modules within the 1756 series. Understanding these compatibility aspects ensures seamless integration and optimal performance within your industrial automation system‚ enhancing overall efficiency.
1756-EN2T and 1756-EN2TR Differences
The 1756-EN2T and 1756-EN2TR are both EtherNet/IP communication modules‚ but a key difference lies in the 1756-EN2TR’s embedded switch‚ which supports features like DLR redundancy. This embedded switch enables the ‘EN2TR’ to handle network redundancy protocols more efficiently than the ‘EN2T’. While the 1756-EN2T serves as a standard EtherNet/IP interface‚ the 1756-EN2TR offers enhanced network management capabilities due to its integrated switch. Selecting between the two depends on the specific network architecture and redundancy requirements of the application. If network resilience is critical‚ the 1756-EN2TR is preferable; Otherwise‚ the 1756-EN2T provides a cost-effective solution for standard EtherNet/IP communication needs.
Integration with ControlLogix Controllers
The 1756-EN2T module is designed for seamless integration with ControlLogix controllers within an EtherNet/IP network. It allows the ControlLogix system to communicate with other devices and systems on the network. During integration‚ the 1756-EN2T module is installed in the ControlLogix chassis and configured using software like RSLinx. This configuration involves setting the IP address and other network parameters. The module then enables the ControlLogix controller to exchange data with devices supporting the EtherNet/IP protocol. Proper integration ensures reliable communication and control across the industrial network‚ enhancing the overall performance and functionality of the ControlLogix system in automation environments. The controller needs to be in Remote Run Mode.
Network Configuration
Network configuration for the 1756-EN2T module involves setting up IP addresses‚ subnet masks‚ and gateway addresses. These settings ensure proper communication within the EtherNet/IP network‚ enabling seamless data exchange and control functionality essential for industrial automation;
IP Address Settings
Configuring the IP address for the 1756-EN2T module is a crucial step in establishing network communication. The IP address must be unique within the network to avoid conflicts. This can be done using software like RSLinx via the USB port. The IP address‚ subnet mask‚ and gateway settings are interrelated and must be correctly configured to match the network’s architecture. Incorrect settings can prevent the module from communicating effectively with other devices. Consider that the gateway address is applicable only to specific modules like 1756-EN2T and 1756-EN2TR. Validate after setting.
Gateway Address Usage
The gateway address is an essential component in the network configuration of the 1756-EN2T module‚ especially when communicating with devices outside the local subnet. It acts as a bridge‚ directing traffic to other networks. This setting is applicable only to certain modules like the 1756-EN2T and 1756-EN2TR. A misconfigured gateway address can isolate the module‚ preventing it from reaching external resources. Ensure that the gateway address is correctly set to the IP address of the network’s gateway router. Verify after setting the gateway address to assure seamless communication across different network segments.
Communication Protocols
The 1756-EN2T module supports EtherNet/IP for industrial automation. It utilizes CIP connections for explicit and implicit messaging. These protocols ensure reliable and efficient communication between the controller and other devices on the network.
EtherNet/IP Protocol Support
The 1756-EN2T module is designed to fully support the EtherNet/IP protocol‚ which is crucial for seamless communication within industrial automation environments. This protocol facilitates real-time data exchange and control functions‚ ensuring efficient operation of connected devices. EtherNet/IP allows the module to integrate effectively with other EtherNet/IP-enabled devices‚ providing a scalable and flexible network architecture. The module’s support for EtherNet/IP extends to various applications‚ including data acquisition‚ process monitoring‚ and remote control. It adheres to industry standards‚ ensuring interoperability and ease of integration. Proper configuration and understanding of EtherNet/IP are essential for maximizing the module’s capabilities. This allows the module to participate effectively in industrial networks.
CIP Connections
The 1756-EN2T module leverages CIP (Common Industrial Protocol) connections to facilitate communication between devices on the EtherNet/IP network; CIP connections are essential for managing data flow and control signals‚ ensuring reliable and efficient operation. The module supports both explicit and implicit CIP connections‚ offering flexibility in how data is exchanged. Explicit connections are typically used for configuration and diagnostics‚ while implicit connections are used for real-time data transfer. The number of CIP connections available on the 1756-EN2T module is limited‚ so it’s crucial to manage them effectively to avoid performance issues. Proper configuration of CIP connections is essential for optimal network performance and reliable data exchange. Understanding CIP connections is crucial for system integrators.